A batch pyrolysis plant has low degrees of automation and as a result, requires a large manual workforce and time for operation. Such a plant needs to be cooled down between different batches of tires, so that residue inside the reactor (steel wire and carbon black) can be collected. Each batch of materials takes 16 to 20 hours to process. So it is more suitable for small scale investors. Taking Beston Machinery for example, the small scale tyre pyrolysis plant can process 6 to 10 tons of raw materials each batch.
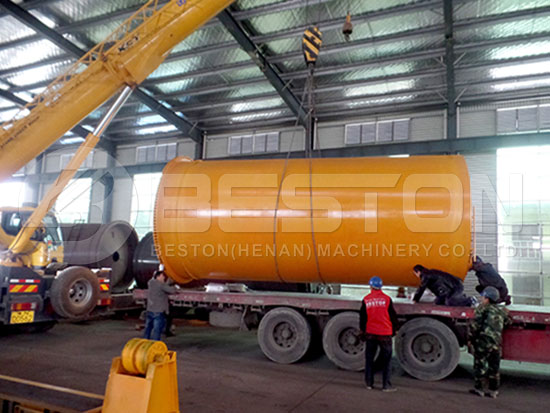
For small local recycling businesses, a batch pyrolysis machine can often meet the processing demands and has the advantage of being more affordable. However, for large-scale waste tire recycling operations, such as government programs and international waste management businesses, a batch pyrolysis plant will be unable to meet the daily processing demands. Such large scale operations require a fully continuous tire pyrolysis plant.
Here are some of the characteristics and benefits of continuous tire pyrolysis plant:
• Precise operational programming calculation to ensure full pyrolysis and maximum oil yield from raw materials. Continuous pyrolysis plant is controlled by PLC control units which calculate and control reactor temperatures and reaction times to ensure all oil in the tires is fully converted into oil gas via pyrolysis reactions.
• Steel wire and carbon black auto-separation system via unique slag design. Modern continuous rubber pyrolysis plants are equipped with unique slag discharge systems to enable automatic separation of steel wire and carbon black from tire rubber inside the reactor. This means operators can save time as steel wire does not have to be manually removed from the shredded tires before they enter the reactor.
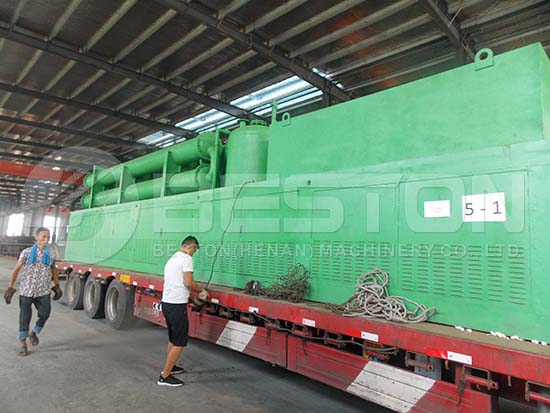
• Fully automatic design. As continuous tire pyrolysis plants are highly automated and can be controlled by a single worker via the PLC console, operational labor costs are very low. The feeding and discharge systems are fully automatic, so no manual labor is required. This means businesses can make very high profits with such plants.
• Large capacity. Continuous waste tire pyrolysis plants have very large hourly processing capacities. Some of the top models can process more than 20 tons of scrap tires every 24 hours. What’s more, they are designed with the smallest possible footprint to optimize floor space requirements for installation. Also, it is building block design, so it is easy to install as well.
• Sealed feed system and discharge system to ensure zero environmental pollution during operation. The unique seal design of high-quality pyrolysis plants ensures no cracked oil or gas can leak through the feed inlet or slag discharge port to guarantee environmental protection. More details can be found on mobile pyrolysis plant here.
As you can see, there are many beneficial features and characteristics of continuous tire pyrolysis plants that make them a better choice than batch plants for a large number of businesses. If you are looking to set up a tire recycling business and plan to convert more than 10 tons of tire rubber to fuel oil, carbon black, steel wire and combustible gas, each day, a continuous pyrolysis machine are almost certain to be the best option. The majority of batch pyrolysis plants can process 10 tons of rubber waste each day at a maximum. If your budget can’t stretch to fully continuous plant design, be sure to research semi-continuous pyrolysis plants. See the pyrolysis plant in the Philippines here.